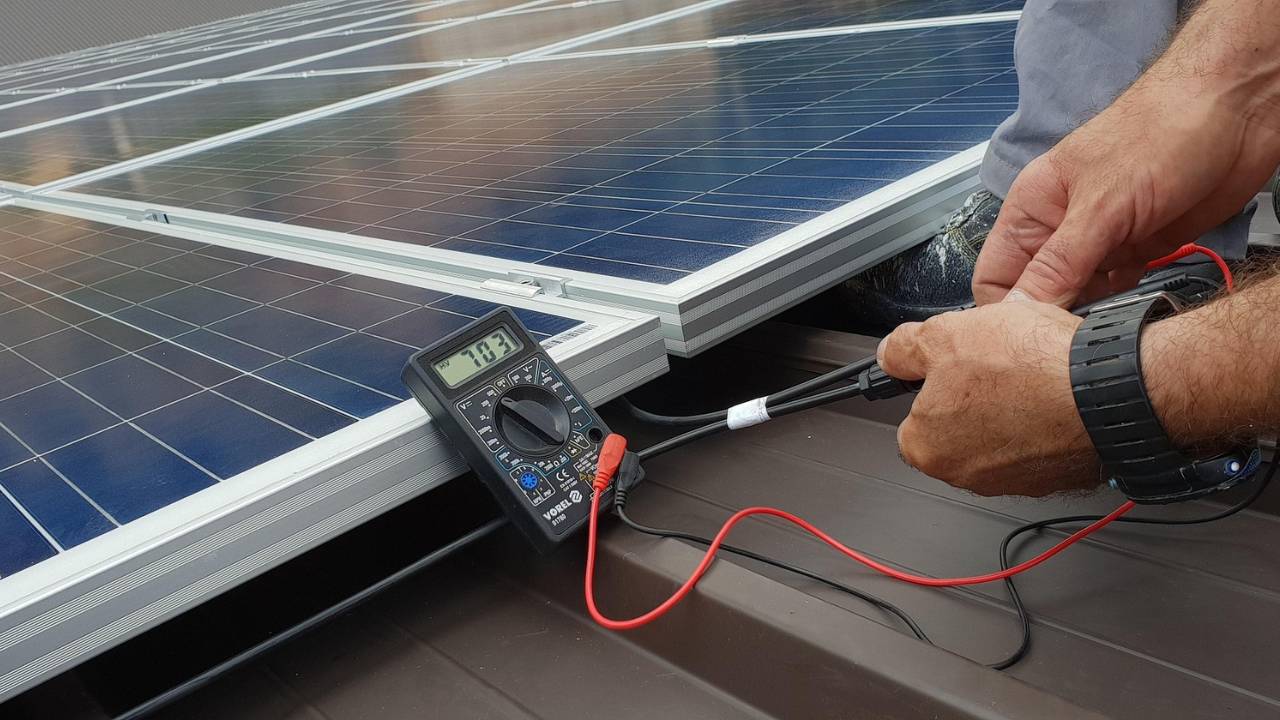
In modern construction and renovation projects, fixed electrical appliances represent a significant component of the final deliverable. These permanently connected installations – ranging from built-in ovens and water heaters to air conditioning systems and hand dryers – require specific safety verification before a project can be properly handed over to clients.
The scrutiny around electrical safety certification has intensified considerably in recent years. This shift reflects both heightened regulatory oversight and growing client awareness of the importance of comprehensive electrical safety documentation. For contractors, the implications are clear: electrical compliance is no longer a box-ticking exercise but a fundamental component of project completion and client acceptance.
Understanding Fixed Appliance Testing Requirements
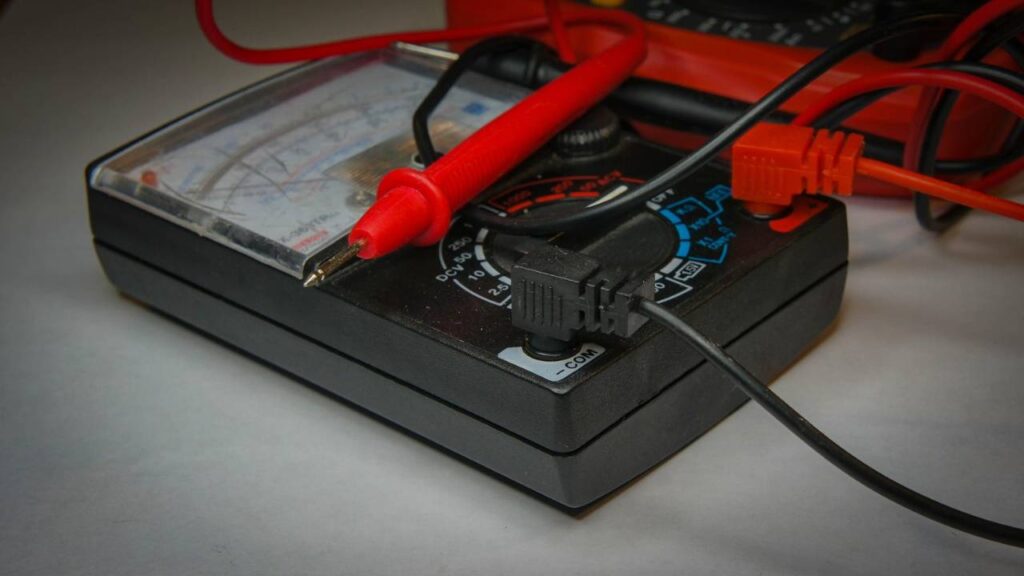
Fixed appliances in the construction context refer to electrical equipment that is permanently connected to the electrical supply (not via a plug and socket) or is effectively immovable due to its size, weight, or attachment to the structure. In Irish construction projects, these typically include:
- Built-in kitchen appliances (ovens, hobs, extractors)
- HVAC systems (air conditioning units, ventilation systems)
- Water heating systems
- Bathroom installations (shower units, hand dryers)
- Fixed lighting systems
- Security and access control equipment
The testing requirements for these appliances differ somewhat from those for portable equipment, reflecting their permanent installation and different risk profiles. Testing is typically required at several stages: after initial installation, before energisation, and during pre-handover inspections.
In Ireland, these requirements fall under the framework of the Safety, Health and Welfare at Work Act 2005 and associated regulations, particularly the Safety, Health and Welfare at Work (General Application) Regulations 2007 (Part 3). These regulations place clear obligations on employers – including contractors – to ensure electrical equipment safety.
Contractors should familiarise themselves with procedures such as PAT testing fixed appliances with Seaward Apollo 600 and other modern PAT testers, ensuring all installed systems meet safety requirements before certification. Modern testing equipment offers significant advantages in terms of efficiency, accuracy, and documentation capabilities, with specialised functions designed specifically for fixed appliance verification.
This is essential not only for compliance but also to promote electrical safety for construction workers who interact with these systems before client occupation. The pre-handover period often involves multiple trades working simultaneously around newly installed systems, creating potential hazards if equipment hasn’t been adequately verified.
The specific tests required typically include:
- Earth continuity testing: Verifies that protective earth connections are intact and have sufficiently low resistance
- Insulation resistance testing: Confirms that insulation between live conductors and earth meets minimum standards
- Polarity verification: Ensures correct connections of line, neutral, and earth conductors
- Functional testing: Confirms that appliances operate as intended when energised
- Leakage current measurement: Verifies that current leakage falls within safe parameters
These tests must be conducted according to manufacturer guidelines and relevant standards, with results documented in a format that satisfies regulatory requirements and client expectations.
Who Can Carry Out PAT Testing, and What Records Are Required?
The question of who can legally perform PAT testing in Ireland causes considerable confusion among contractors. While the regulations don’t specifically require that all testing be performed by registered electricians, they do stipulate that work must be carried out by a “competent person” with appropriate knowledge, training, and experience.
For complex fixed installations, this typically means:
- Registered electrical contractors (RECs) registered with Safe Electric
- Qualified electricians with specific training in testing procedures
- Technical personnel who have completed recognised PAT testing certification courses
Many contractors find that the most practical approach involves a combination of in-house capabilities and specialist partners. Having key team members trained in basic testing allows for preliminary verification while engaging certified electrical contractors for final testing and documentation provides additional assurance.
The record-keeping requirements are equally important. Comprehensive documentation should include:
- Test certificates for each appliance or system, identified by unique reference numbers
- Photographic evidence of tested installations (increasingly expected by clients)
- Details of any remedial work required and subsequently completed
- Calibration certificates for test equipment used
- Qualifications and credentials of personnel conducting the tests
These records should be compiled into a comprehensive electrical safety file as part of the project handover documentation. Increasingly, clients expect digital versions of these records in addition to hard copies, facilitating future maintenance and inspection schedules.
Common Fixed Appliances That Require Testing Before Handover
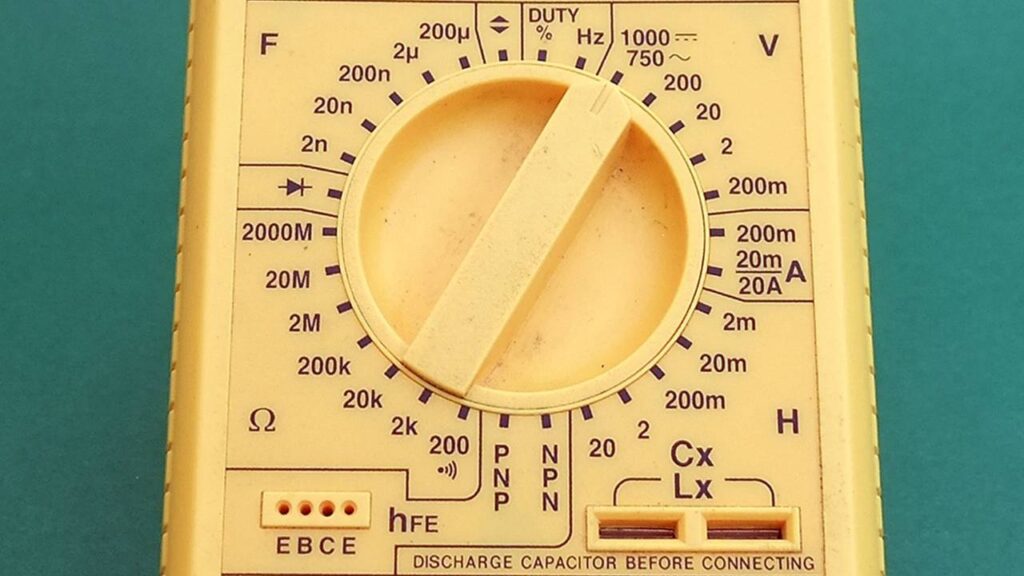
The scope of fixed appliance testing extends across numerous systems installed during construction projects. Common examples include:
- Kitchen installations:
- Built-in ovens and hobs
- Integrated refrigerators and freezers
- Dishwashers and waste disposal units
- Extractor hoods and ventilation systems
- Bathroom fixtures:
- Electric shower units
- Heated towel rails
- Hand dryers
- Extractor fans
- Climate control systems:
- Air conditioning units
- Electric heaters and radiators
- Underfloor heating systems
- Heat recovery ventilation
- Building services:
- Water pumps and circulation systems
- Lift and elevator systems
- Access control equipment
- Emergency lighting
- External installations:
- Outdoor lighting systems
- Gate and barrier operators
- CCTV and security equipment
- Irrigation systems
It’s important to distinguish between the testing responsibilities for fixed versus portable appliances. While portable appliance testing (PAT) focuses on equipment with plugs that connect to standard outlets, fixed appliance testing addresses permanently connected equipment. In many projects, both types of testing will be required, but they involve different procedures and sometimes different personnel.
Integrating Testing into Your Project Timeline
One of the most common pitfalls in construction projects is leaving fixed appliance testing until the last minute. This approach invariably leads to unnecessary pressure, potential delays, and increased costs if issues are identified. A more strategic approach involves integrating testing throughout the project timeline.
Effective integration might include:
- Design phase: Identify all fixed electrical appliances that will require testing and certification.
- Pre-installation: Verify that specified appliances meet relevant safety standards and have appropriate documentation from manufacturers.
- During installation: Conduct preliminary testing of connections and safety features before full energisation.
- Post-installation: Perform comprehensive testing as each system is completed, rather than waiting until all installations are finished.
- Pre-handover: Conduct final verification and compile all documentation into a comprehensive safety file.
This phased approach allows for early identification of issues when they are easier and less costly to address. It also distributes the testing workload more evenly throughout the project, reducing pressure during the critical pre-handover period.
The testing schedule should be explicitly included in project programs and quality assurance workflows. Many contractors now include electrical testing as a specific milestone that must be signed off before subsequent work can proceed. This approach prevents situations where issues are discovered after decorative finishes have been applied, requiring disruptive and expensive remedial work.
Training and Safety Culture on Site
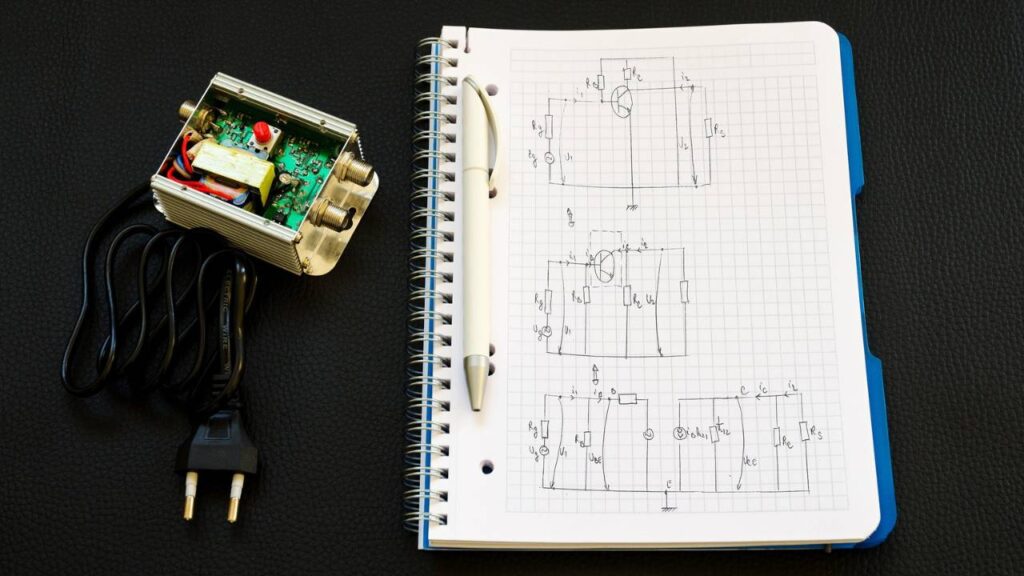
Beyond the technical aspects of testing, successful contractors recognise the importance of developing a strong electrical safety culture across their entire workforce. When all team members understand basic electrical safety principles, they’re better equipped to identify potential issues during installation and prevent problems that might only be discovered during formal testing.
Promoting the importance of electrical safety training for employees ensures everyone on site can identify hazards and take proactive safety steps – well before testing even begins. This proactive approach transforms safety from a compliance exercise into a core operational principle.
Effective training approaches include:
- Toolbox talks specifically addressing electrical safety issues
- Visual guides posted in work areas highlighting common electrical hazards
- Clear protocols for reporting potential electrical issues
- Recognition programs that reward safety-conscious behavior
Many contractors find that investing in basic PAT testing training for non-electrical personnel – such as site managers, quality inspectors, and lead tradespeople – pays significant dividends. While these team members won’t perform official testing, their awareness helps maintain safety standards throughout the project and identifies potential issues earlier.
The benefits extend beyond the immediate project. Contractors with established safety cultures and verifiable training programs often gain competitive advantages in tender situations, particularly for clients with strict safety requirements or previous experiences with electrical compliance issues.
Conclusion: Safer Sites, Smoother Handover
Fixed appliance testing is a vital part of delivering safe, compliant, and client-ready construction projects. By integrating proper testing procedures early, working with qualified personnel, and maintaining clear documentation, contractors can avoid last-minute surprises and ensure all systems meet regulatory and safety standards.
Beyond compliance, this proactive approach enhances worker safety, builds client trust, and protects your business from costly delays or liability. Embedding fixed appliance testing into your project workflow is not just best practice – it’s a strategic move toward smoother handovers and a stronger professional reputation.