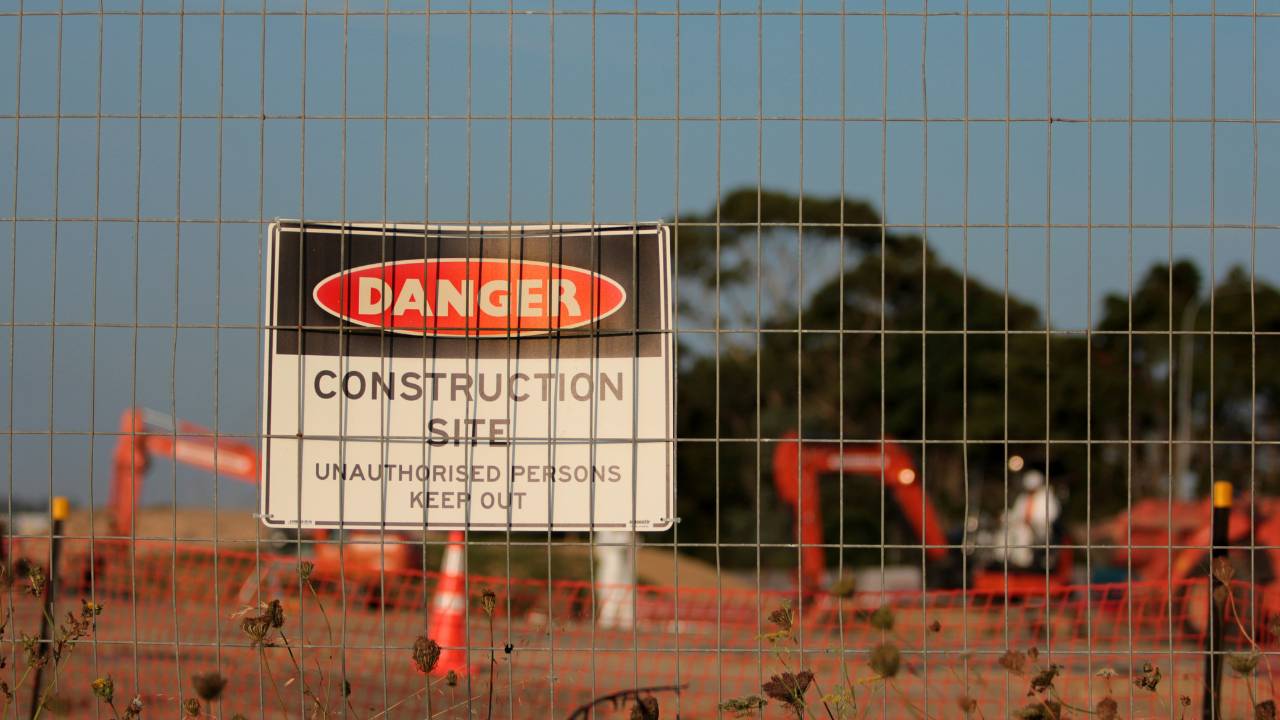
Accidents in the construction industry can have devastating outcomes, making workplace safety a top priority for employers and employees alike. Lockout/Tagout procedures play a crucial role in safeguarding construction workers from hazardous energy releases while maintaining equipment. The implementation of these procedures ensures that machinery is properly shut down and not restarted until completion of maintenance or repair work, thereby preventing accidental injuries and fatalities.
In recent years, increased attention towards compliance with safety standards has highlighted the importance of Lockout/Tagout practices. Following these procedures not only protects workers but also aligns with legal requirements set by regulatory bodies. This adherence to safety laws reflects a commitment to protecting personnel, fostering a safer working environment, and reducing the chance of operational disruptions.
Adopting Lockout/Tagout protocols in the construction sector signifies a proactive approach to risk management. By investing in proper training and tools, companies demonstrate an emphasis on the well-being of their workforce. This preventive strategy not only reduces potential hazards but also builds a culture of safety that prioritises human life above all else.
Understanding Lockout/Tagout (LOTO)
Lockout/Tagout (LOTO) is crucial for ensuring worker safety in construction by controlling hazardous energy. Implementing LOTO procedures helps prevent accidents caused by unexpected energy release during maintenance and repair tasks.
Defining Lockout and Tagout
Lockout involves isolating machinery or equipment from energy sources to prevent accidental operation. It entails applying locks to power switches or valves, physically keeping them in an off position. This method ensures that no accidental start-ups occur during maintenance.
Tagout, meanwhile, uses warning tags or labels on power switches or valves to inform personnel that the equipment is being worked on and must not be operated. Tags provide essential information but rely on awareness rather than physical restraint.
Together, these methods play a critical role in preventing lockout tagout mistakes leading to injury or death.
Importance of Locking Out Hazardous Energy Sources
Controlling hazardous energy is vital for worker safety during equipment maintenance. Failure to properly lock out energy sources can result in catastrophic accidents.
Serious injuries may occur if machinery starts unexpectedly due to a lack of energy isolation. Lockout procedures provide a physical safeguard against the release of stored energy, ensuring that equipment remains safely inoperative while being serviced.
This protection is particularly essential in environments where equipment has multiple energy sources or complex energy distribution systems.
The Differences Between Lockout and Tagout Procedures
The primary difference between lockout and tagout is the level of security each provides. Lockout offers a physical barrier, making it the more secure option. It requires personnel to use locks that prevent the operation of machinery until the lock is removed.
Tagout, in contrast, relies on providing visual cues through tags. While these tags inform and alert workers to the presence of ongoing maintenance, they do not offer physical deterrence. In situations where locks cannot be applied, additional measures such as blockades or chains may accompany tagout procedures to enhance safety.
LOTO Procedures and Compliance
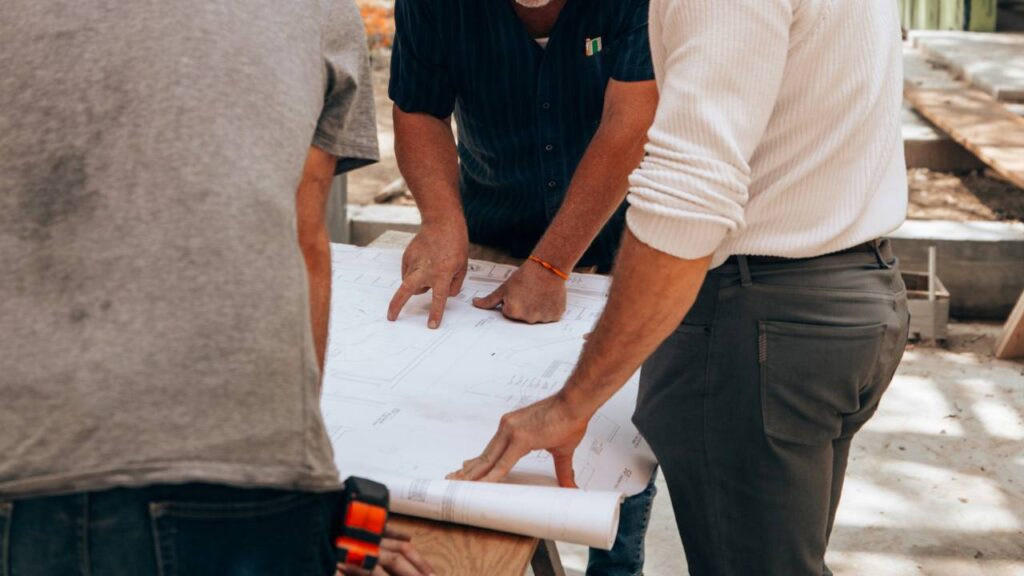
Lockout/Tagout (LOTO) procedures are an essential safety component in the construction industry. Ensuring compliance with these procedures and regulations is critical for worker safety and operational efficiency. Regular audits and continuous improvement efforts also play a crucial role in maintaining high safety standards.
Developing Effective LOTO Procedures
To create robust LOTO procedures, an organisation must first identify all potential energy sources within a site. This includes electrical, hydraulic, pneumatic, and mechanical systems. Each energy source should have clearly outlined steps for isolating and locking out the system to prevent accidental energisation.
Clearly defined roles and responsibilities are vital. Workers need comprehensive training to understand the nuances of LOTO procedures. Documentation is also essential to ensure each step is correctly followed. Information such as equipment-specific instructions and permits should be readily accessible. Using clear visual cues, such as distinct tags and locks, can greatly enhance understanding and adherence.
Compliance with Regulations
Regulatory compliance is mandatory in construction, encompassing stringent guidelines specific to LOTO processes. Organisations must align with the Health and Safety Executive (HSE) regulations or any relevant authoritative body governing their operation. Adherence ensures that all LOTO procedures meet the prescribed safety standards and legal requirements.
Maintaining compliance involves regular updates to protocols to reflect changes in regulations. It also requires that employees are well-informed of current standards through ongoing training and communication. Failure to comply can result in severe consequences, including legal penalties and increased risk of workplace accidents.
Regular Audits and Continuous Improvement
Conducting regular audits is an essential practice for verifying the efficacy of LOTO procedures. These audits should evaluate all aspects, including procedural adherence, employee competence, and equipment condition. Audits provide an opportunity to identify gaps or inefficiencies in current practices.
Continuous improvement stems from the findings of these audits. Organisations must be willing to adjust procedures and training programmes to enhance safety outcomes. Actively seeking employee feedback can contribute to more effective strategies. By fostering an environment of ongoing learning and refinement, an organisation can better protect its workers and uphold industry standards.
Risk Assessment and Energy Control
Implementing effective risk assessment and energy control measures is crucial in construction. Understanding and managing the dangers associated with energy sources help prevent accidents and maintain a safe working environment.
Identifying and Assessing Risks
Risk assessment involves identifying potential hazards in the work environment. Construction sites often face risks from electrical, hydraulic, and mechanical energy sources. Identifying these hazards requires careful evaluation of equipment and processes.
Personnel must examine energy types, sources, and methods of transfer. Evaluations should consider possible failures and maintenance issues. Accurate risk assessments are essential for implementing robust lockout/tagout procedures tailored to specific site conditions. Regular reviews ensure existing measures remain effective and adapt to any changes in the work environment.
Methods of Energy Control
Energy control is vital in preventing unauthorized energy release. The lockout/tagout procedures help achieve this by isolating equipment from energy sources. Personnel must follow established protocols to ensure all equipment is in a zero-energy state before work begins.
Common methods involve de-energising systems and preventing accidental reactivation. Using physical locks and tags clearly communicates when equipment should not be operated. Detailed documentation of energy control procedures ensures everyone in the workplace knows when and how to safely engage and disengage equipment, reducing the risk of accidents.
Energy Isolating Devices
Energy isolating devices play a crucial role in preventing unintended energy flow. These devices physically disconnect machinery from energy sources, providing an important safety layer in construction projects. They can include circuit breakers, valves, and other mechanisms that ensure machinery remains inert during maintenance or repair.
Proper implementation of these devices is essential. Workers should regularly inspect and maintain them to guarantee functionality. Clear labelling and secure placement prevent misuse or accidental engagement. By employing energy isolating devices effectively, construction teams significantly reduce risks and enhance occupational safety. They serve as an essential component of a general energy control strategy, safeguarding both personnel and equipment.
Devices and Tools for LOTO
Lockout/Tagout, commonly referred to as LOTO, involves various devices and tools to ensure the safe de-energisation of machinery and equipment during maintenance. Different types of lockout devices secure energy isolation points, while tagout devices provide essential visual warnings. Lockout hasps and padlocks play crucial roles in ensuring comprehensive safety.
Types of Lockout Devices
Lockout devices prevent the release of energy by isolating equipment during critical operations. They vary in design to fit different energy sources, such as electrical, hydraulic, and pneumatic systems. Common devices include valve lockouts, which secure pipelines, and lock boxes, suitable for managing multiple lockout points.
These devices must be robust and tamper-proof to be effective. Adjustable and universal models offer adaptability and cater to various machinery specifications. Selection depends on the specific needs and types of energy sources present on a construction site. The proper use of these devices is fundamental in preventing accidental equipment start-up.
Application of Tagout Devices
Tagout devices serve as visual indicators warning personnel not to operate machinery. They accompany lockout devices to provide a comprehensive safety system. Each tag typically displays essential information, such as the name of the authorised personnel and the date of application, enhancing accountability.
The use of durable materials ensures that tags remain legible in construction environments. While they do not provide physical restraint, they are vital in conveying safety messages and procedures. Effective application requires clear communication and training, ensuring all workers understand the significance of these tags in maintaining a safe environment.
Use of Lockout Hasps and Padlocks
Lockout hasps and padlocks allow multiple workers to lock out a single energy source securely. Hasps enable the attachment of several padlocks, ensuring no single person can remove a lock and re-energise equipment without the knowledge of all parties involved. This ensures collective safety among team members.
Padlocks are distinguished by their unique keys or codes, ensuring each worker’s lock can only be removed by them. They are often used in combination with hasps in situations where collaborative work is necessary. The combination of these tools creates a layer of safety, essential for maintaining strict control over potentially hazardous energy sources during maintenance or repairs.
Worker Safety and Training
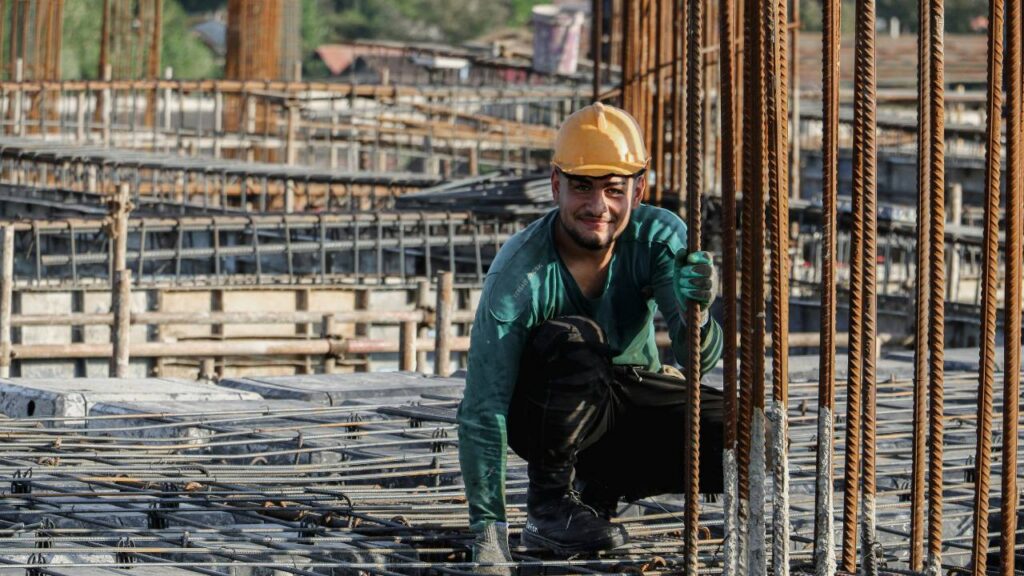
Highlighting the importance of meticulous safety protocols and thorough training is crucial in construction. Lockout/Tagout (LOTO) procedures enhance worker safety, preventing accidents. LOTO training requirements are crucial for effective implementation, while fostering a strong safety culture ensures ongoing commitment.
Implementing Safety Protocols
Implementing rigorous safety protocols is essential for protecting construction workers. These protocols include proper maintenance of machinery and clear communication regarding potential hazards.
Lockout/Tagout procedures are vital in preventing accidental machinery startup. Workers must isolate energy sources before performing maintenance tasks. Regular audits and inspections ensure adherence to these protocols. Thorough documentation of procedures, combined with regular reviews, sustains high safety standards. Protocols also require worker collaboration, enhancing overall compliance and minimising risks effectively.
LOTO Training Requirements
Adequate training is fundamental for effective Lockout/Tagout implementation. Workers must understand the significance of each step in the procedure to ensure workplace safety. Training programmes should cover identifying hazardous energy sources, proper lockout equipment use, and step-by-step protocol execution.
Training sessions must incorporate both theoretical knowledge and practical exercises. Regular refresher courses update workers on new technology and amendments in safety regulations. Supervisors play a crucial role in monitoring and assessing the effectiveness of these training programmes. Comprehensive LOTO training empowers workers to perform tasks safely and efficiently, mitigating risks associated with electrical and mechanical hazards.
Fostering a Safety Culture in the Workplace
Establishing a robust safety culture is indispensable for sustaining worker safety. Management commitment is pivotal in promoting safety initiatives and setting a responsible example. Open communication channels encourage workers to report safety concerns without fear of repercussions.
Engagement in regular safety meetings reinforces the significance of following safety protocols and encourages proactive participation from all employees. Reward systems for adherence to safety protocols can motivate workers to prioritise safety consistently. Collaboration between workers and management fosters a united approach to minimising workplace risks, creating a safer work environment for everyone involved.
Group Lockout Best Practices
Implementing group lockout procedures effectively requires meticulous planning, robust communication, and an unwavering focus on safety. Teams must coordinate their efforts seamlessly, ensuring all members are aware of their roles, responsibilities and the status of equipment during lockouts.
Coordinating Lockouts in Teams
Efficient teamwork starts with clear role allocation. Each team member must understand their responsibilities, which may vary based on skill level and experience. This approach minimises errors and ensures efficiency. Training plays a crucial part in keeping everyone informed about lockout steps and procedures.
Regular checklists and protocols help manage each lockout session. Every participant should be aware of the equipment involved, the location of all locks, and the sequence of operations. Documentation of these practices helps maintain consistency across different projects and sites, serving as a reference in case any issues arise.
Communication and Ties in Group Lockout
Effective communication is fundamental to safe group lockouts. It is essential to establish standard communication channels where team members can exchange information quickly and reliably. This can be facilitated through regular team meetings and updates via secure, closed communication systems.
Identification of key persons responsible for specific tasks helps alleviate confusion. By designating a lead communicator, teams can manage the dissemination of critical information, ensuring every member is on the same page. Additionally, clear and visible labelling of lockout devices and control panels aids in averting misunderstandings.
Maintaining Safety During Group Lockouts
Safety is paramount at all stages of group lockout. Implementing safeguard checks before and during lockouts can prevent accidents. Before initializing a lockout, each member should inspect the site thoroughly to assess any hazards that must be mitigated.
Mandatory safety gear enhances protection during operations, and it is necessary for all personnel involved in the lockout process. Regular safety drills reinforce the importance of safety practices, ensuring everyone knows how to respond in emergencies.
Record-keeping of safety incidents, if any occur, is an essential practice, providing insights for future prevention measures. Equip the team with resources that focus on maintaining a zero-tolerance attitude towards safety violations, ensuring a secure environment for all involved.
Dealing with Residual and Stored Energy
In construction, ensuring safety involves addressing the complexities of residual and stored energy. These energy forms can lead to unforeseen hazards if not properly managed. Understanding the dynamics of this energy is critical to preventing accidents and maintaining a secure work environment.
Mitigating Risks from Residual Energy
Residual energy refers to energy that remains in a system even after it has been turned off. It is often caused by electrical charge, hydraulic pressure, or thermal heat. Mitigating risks associated with this energy requires proper de-energisation techniques.
Workers need to discharge capacitors and release trapped energy by using appropriate tools. Following a strict protocol for dissipating this energy can significantly reduce accident risks. Training plays a crucial role; workers must understand how residual energy can manifest and how to safely address it.
Regular equipment inspections help in identifying leaking valves or faulty components that might retain energy. Not adhering to these practices can lead to severe consequences such as accidental activation of machinery, posing a threat to worker safety. By ensuring all systems are fully de-energised, construction industries can enhance safety.
Handling Kinetic and Potential Energy
Kinetic energy is the energy of motion, while potential energy is stored within an object due to its position. Both forms can be hazardous if not properly controlled. Equipment can move unexpectedly, leading to injuries; hence, understanding these energies is vital.
Properly securing or supporting equipment with blocks or restraints prevents unintended movement. Awareness of gravitational potential can help in preventing falls or drops during operations. Machinery with rotational parts requires special attention to prevent kinetic release.
Training is essential in recognising situations where kinetic and potential energies might be present. Workers should be versed in strategies to neutralise these energies, ensuring stability during construction activities and contributing to a safer working environment.
Lockout Considerations for Stored Energy
The lockout process is essential for neutralising stored energy, which might be chemical, mechanical, or electrical. Proper lockout/tagout procedures ensure that energy cannot be released while maintenance or repairs are conducted.
Maintaining clear communication and employing multiple lockout devices can prevent accidental energy release. Understanding the stored energy’s nature helps in applying the appropriate lockout techniques. Periodic review and updating of lockout procedures are essential for staying compliant with safety regulations.
A robust lockout system removes the uncertainty around stored energy, safeguarding workers and machinery. By adhering to these practices, construction sites can minimise risks associated with unexpected energy release, thereby prioritising worker safety.
Maintenance, Repairs, and Accident Prevention
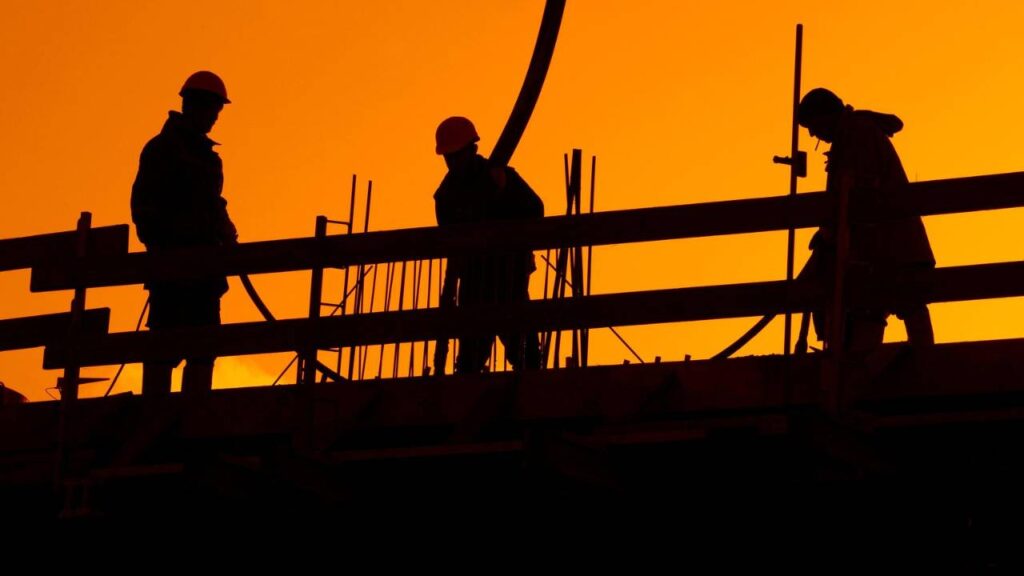
Ensuring safety in maintenance and repair operations is critical to preventing accidents and severe injuries. By implementing robust Lockout/Tagout (LOTO) procedures, the risk of unexpected equipment startup is significantly reduced.
LOTO in Maintenance and Repair Operations
In construction, LOTO procedures are vital during maintenance and repair activities. These procedures involve disconnecting power sources and securing machinery to prevent accidental restorations during service tasks.
LOTO training for workers ensures they understand their roles in the process, helping prevent injuries. Safety controls, including strict authorisation and communication protocols, are essential. Workers should consistently validate that lockout devices are operational before commencing work.
Independent verification by another certified individual confirms compliance, fostering a culture of safety.
Strategies to Prevent Unexpected Equipment Startup
Preventing accidental machine activation requires multi-layered strategies. Regular maintenance of equipment and control panels is key, reducing chances of malfunctions.
Implementing procedural checklists also fosters adherence to safety standards. Proper signage, denoting machines under maintenance, makes hazards clear to all personnel. Remote energy isolation systems provide an additional layer of safety by allowing equipment to be safely powered down from a distance.
Creating a structured environment where workers feel accountable and empowered to report safety concerns further minimises risks.
Measures to Avert Severe Injuries
Promoting a safe work environment involves stringent measures against severe injuries. Adequate personal protective equipment (PPE), tailored to specific tasks, reduces exposure to hazards. Ongoing training sessions keep the workforce updated on new safety protocols and best practices.
Emergency response plans, regularly updated and rehearsed, prepare teams for rapid reaction in case of an accident. Regular audits and inspections validate the effectiveness of these measures, identifying potential for improvement in safety systems.
Awareness campaigns highlighting the human and financial costs of injuries also contribute to a culture of safety.
Conclusion
Implementing lockout/tagout procedures is critical in the construction industry. These practices are essential for ensuring worker safety, as they prevent unexpected equipment start-ups during maintenance. By following these procedures, construction firms can significantly reduce the risk of accidents.
Lockout/tagout processes are not just about safety; they also serve to mitigate legal risks in construction. Adherence to these protocols demonstrates a commitment to regulatory compliance, thereby safeguarding companies from potential legal repercussions.
Workers must be trained in these procedures, reinforcing their importance and ensuring consistency. Regular auditing of these practices can help identify areas for improvement, fostering a safer work environment.
To conclude, the integration of lockout/tagout systems into daily operations is not merely a recommendation, but a necessity for safer and more compliant construction practices.